Content Attributes
Previous engineers and architects would take time to use pen and paper to draw a concept desired by their clients. Even if you manage to do a three-dimensional drawing, its representation would need extensive translation to understand fully. Advances in technology have changed all this. You can make digital representations of physical objects, thus making them easier to grasp. It is what digital twin technology brings. But what is this technology, and how does it work? Read on for this insight.
What Is Digital Twin Technology?
Digital twin technology creates a virtual representation of a real-life project, thus enabling engineers to measure, monitor, and improve its performance. Its use spans several industries like manufacturing, health, and energy sectors. You can also find digital twin for road corridors or city planning.
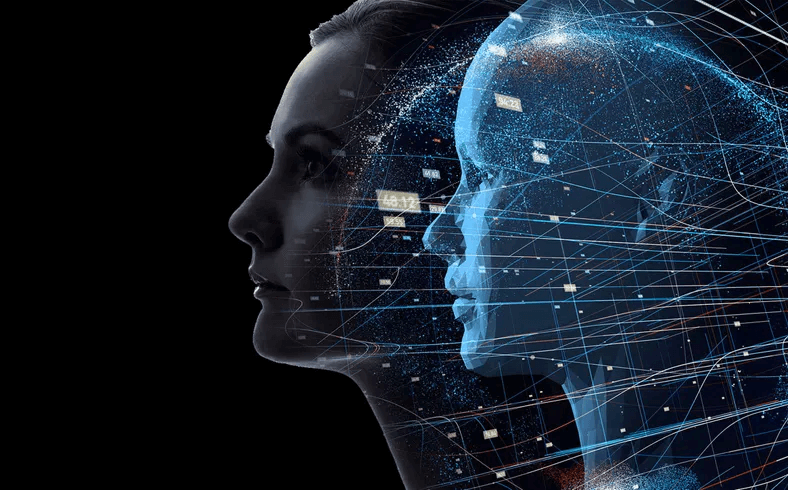
Digital twin technology ensures that you can deploy a physical product once it satisfies parameters instead of testing a prototype in real life, failing, and then starting over again. It’s also important to note that digital twin technology help to monitor projects in a live environment. Thus, engineers can assess and make improvements in a predictive maintenance process.
How does Digital Twin Technology Works?
The evolvement of industry 4.0 brings together the internet of things (IoT), big data, and cloud computing technologies. These form the essential tech that enables engineers to build a virtual copy of the actual product.
Sensors are strategically connected to the real object to develop a virtual copy. These sensors collect various data, which is then uploaded to an IoT platform. After which, you can use artificial intelligence (AI) or machine learning (ML) algorithms to process the data. The data processing enables you to analyze, develop, and measure various scenarios to determine an outcome for your project.
The Functions Of Digital Twin Technology
Most experts attribute the popularity of digital twin technology to its three primary functions: monitoring, analyzing, and optimizing performance. You might find these functions referred to as the see, think, and do purposes of digital twin tech.
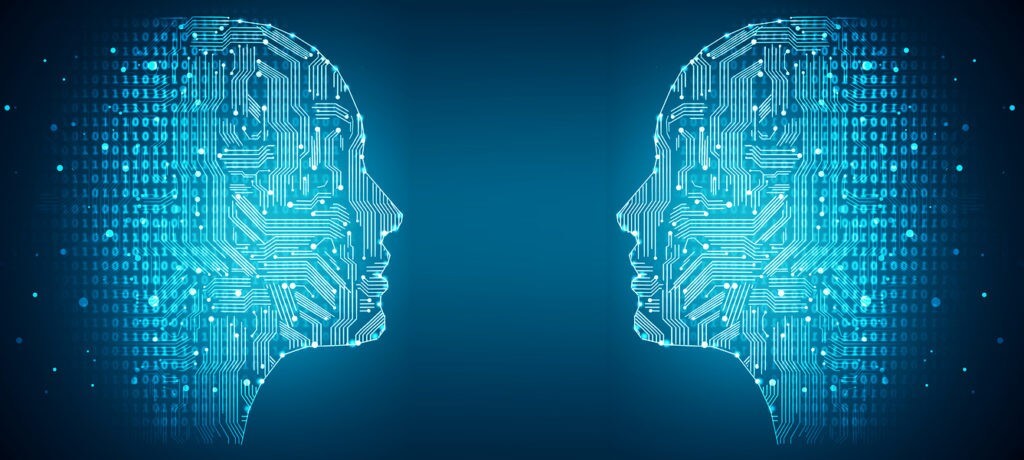
The Basic Level
At the basic level, digital twin technology visualizes the existing situation. This function uses data from the sensors connected to the actual objects. Production engineers can use this data to see how a product performs in the physical environment.
The Middle Level
Data from the monitoring level is essential to the analysis level. On this level, digital twin technology processes the data by subjecting it to various scenarios or operational settings. These exposures give the analysts different possible outcomes from each environment.
The Advanced Level
At the optimization level, this function of the digital twin technology detects issues arising from the different outcomes from the analysis level. Additionally, it identifies alternative solutions to these issues. Depending on the algorithm, the digital twin technology will provide the most preferable or appropriate solution. This solution is then automatically implemented.
In summary, digital twin technology enables you to collect relevant data for analysis and virtually monitor an object in the real world. The middle level gives you various outcomes in different environments. From these outcomes, predictive maintenance algorithms show you what to do to make improvements or changes.
Types Of Digital Twin Technology
The type of digital twin technology you choose should depend on your required virtual model. For instance, a digital twin prototype (DTP) is for a product that’s not yet on the market. Thus, you’re using DTP to design and analyze the product in the virtual realm. It enables you to test the success or fail rate of the product before commencing physical production. This digital twin technology type can help production engineers reduce costs and deployment time.
On the other hand, a digital twin instance (DTI) is a type that is connected to an active physical product. Thus, it provides feedback on the performance and maintenance requirements of the product. Engineers can use the feedback data to do preventative maintenance. Therefore, it helps avoid unnecessary downtime.
Finally, the digital twin aggregate (DTA) is a collection of various virtual models under DTPs and DTIs. These models help collect bulk data from several products and compare each under varied conditions. This type gives a broad insight into the physical product’s behavior and optimization alternatives.
Benefits Of Digital Twin Technology
One of the significant benefits of digital twin technology is its effect on production cost. The previous production processes would require live testing of a prototype. However, digital twin technology enables the production crew to run tests and simulations virtually. It’s easier and faster to make adjustments in a virtual setup than in a real one. Thus, it reduces the production cost by a significant margin.
Running tests and performances virtually also reduces the time required to go live with a new product. Subjecting the digital prototype to virtual simulations enables you to make changes faster and easier to make a product viable. Thus, you can deploy them within a short period. Consequently, it helps you create a reliable product that your customers can enjoy.
Conclusion
Digital twin technology provides a virtual setup that enables you to create a digital representation of a process, product, or service. It utilizes the concepts of IoT, big data, and cloud computing. Thus, allowing you to monitor, analyze, and optimize your project under various conditions.