Content Attributes
Centrifugal Wood Pellet Machine 8th Gen Biomass Pellet Machine
A type of Pellet Machines that is frequently used in the biomass energy sector is indeed the biomass pellet machine. To replace coal, a new kind of fuel molding machine smashes biomass raw materials like tree branches & straws in rod-shaped particles.
The two types of biomass pellet machines are flat die and ring die. Vertical centrifugal super high-performance ring die biomass pellet machine combines the benefits of conventional horizontal ring die & flat die pellet machines, so it is particularly well suited for biomass pelleting.
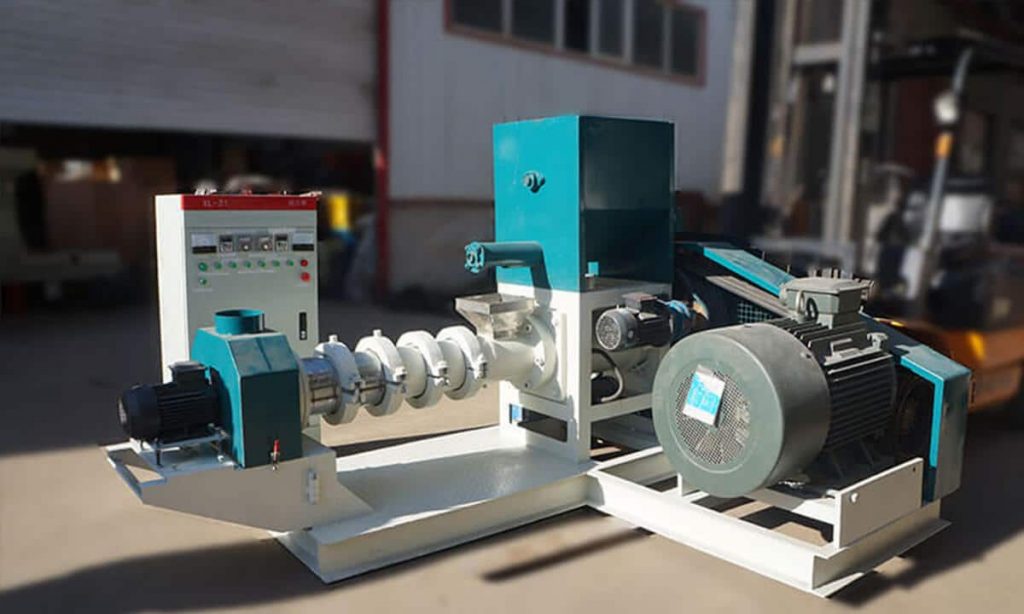
Benefits of using our biomass pellets mill
- The pellet machine, lubricating oil pump, dust collector, as well as electrical control cabinet, make up the bulk of a biomass pellet machine.
- The throughput is 1.5 to 2 tonnes per hour, and the power is 132KW. The gearbox and motor are intimately coupled to boost production effectiveness and the pace at which kinetic energy is converted.
Technical advantages
The gearbox uses a 3 stage gear reduction, and it has an extremely long service life and a carrying capacity that is five times greater than the old type. The gear shaft bearing has an adjustable construction, allowing for long-term wear and tear without having to unload the machine.
The gearbox has a lubricating cooling system that allows the machine to continue running while the lubricating oil is cooled, assuring long-term performance. To efficiently avoid equipment problems brought on by inadequate lubrication, the gear lubrication system is fitted with flow sensing and overpressure prevention.
New Feed system
The tray’s problem of being quickly corroded by hot steam is entirely resolved by the exterior positioning of the tray. It is a significant advancement for the biomass pellet machine of the eighth generation.
The material transfer cover’s non-moving components that come into interaction with materials and steam, except the production and transport turntable, are entirely constructed of stainless steel, thereby resolving the issue of metal material corrosion.
Mould and Pressure
- Core component-ring die: made of wear-resistant stainless steel & quenched in a vacuum furnace, the dies have a consistent hardness, no damage, and are extremely resistant to wear. Die holes are processed using a high-speed gun drill, and the interior of the holes is smooth.
- The roller, which is the main component, uses super wear-resistant alloy welding technology in place of the prior surface carburizing process. Long service life while being aware of ring die protection.
Centrifugal Wood Pellet Mill 8th Gen
A type of pellet equipment that is frequently used in the biomass energy sector is the biomass pellet machine. A new kind of fuel-producing device called a biomass pellet mill turns biomass resources like tree branches & straws into rod-shaped pellets to replace coal.
The two types of biomass pellet machines are flat die and ring die. Our company’s vertical centrifugal high-performance ring die pellet machine combines the benefits of conventional horizontal ring die and flat die pellet machines, and it is particularly well suited for pelleting biomass.
Some main Advantages
- The primary motor is changed to a conventional flat key motor, and the German KTR elastic coupling is used with the reducer, which fixes the issue of the seven-generation biomass pellet machine’s spline requiring frequent lubricating grease. Additionally, KTR elastomeric repair costs are significantly cheaper than that following spline damage.
- The placement of the spindle frame plate, as well as the spindle, has been improved and upgraded; the pin positioning, which is difficult to disassemble and is prone to wear, has been eliminated, and the CNC machining technique of embedded positioning, which is simple to disassemble and resistant to wear, has been adopted.
- Improvement to the kick-out system: A cycloidal pinwheel reducer to a hard tooth surface reducer has been installed instead of the kick-out plate reducer. The kick-out system’s vulnerability to high temps steam is fully eliminated since the spinning parts of the kick-out mechanism are entirely isolated from the kick-out boot (the whole driving process takes place outside). In addition, stainless steel is used for all of the stationary components in the kick-out boot of the pellet machine, except the kick-out turntable, which essentially eliminates the corrosion issue with metal materials.