Content Attributes
A non-contact method called laser welding enables the assembly of metal components primarily using a laser beam. This kind of welding is appropriate for tasks that call for rapid welding and narrow seams with less thermal deformation. Laser welding is a widely utilized technique in various industrial sectors, including the medical industry, electronics, tool manufacturing, and the automotive industry, due to its speed, capacity to manage the quality of welding during welding, and high level of automation.
Why go for a laser welding device?
The following are some benefits of laser welding machines:
They move quickly
The laser of the laser welding machine minimizes the possibility of deformation while permitting exceptionally rapid heating of the metal.
This method is commonly utilized in the automobile sector. Because it works particularly well for welding massive amounts of sheet metal.
They are also quite precise
They provide a focused, pinpointed, incredibly clean, nearly undetectable welding. It is very well suited for welding tiny components. This kind of welding offers the most aesthetically pleasing welding and is particularly popular in the jeweler and dentistry sectors. To enable even more precise welding, it is also possible to divide the laser beam into several beams.
They may be modified to work with a broad range of component forms and materials
Metals, especially refractory metals, are often welded using laser welding devices. They can also be used to join non-metallic components, such as glass and porcelain, together. It may be used to weld components with a wide variety of forms.
They are durable:
Laser welding devices work without making touch, thus there is no chance of equipment damage.
In terms of waste reduction, there is also no requirement to switch out tools or electrodes.
Orders can be sent to them digitally:
It is now feasible to manage the welding process‘ welding quality from a computer. Such a procedure also enables a high level of automation, making it easier to identify and address any quality issues.
But it should be remembered that laser welding equipment also has certain drawbacks:
- Installing laser technology still carries a hefty price tag.
- To prevent laser beam deflections on the pieces during processing, this method demands extremely accurate assembly.
- Because the laser weld is smaller than the one produced by electron beams, welding highly reflective metal cannot be done using this method.
benefits of laser welding machines
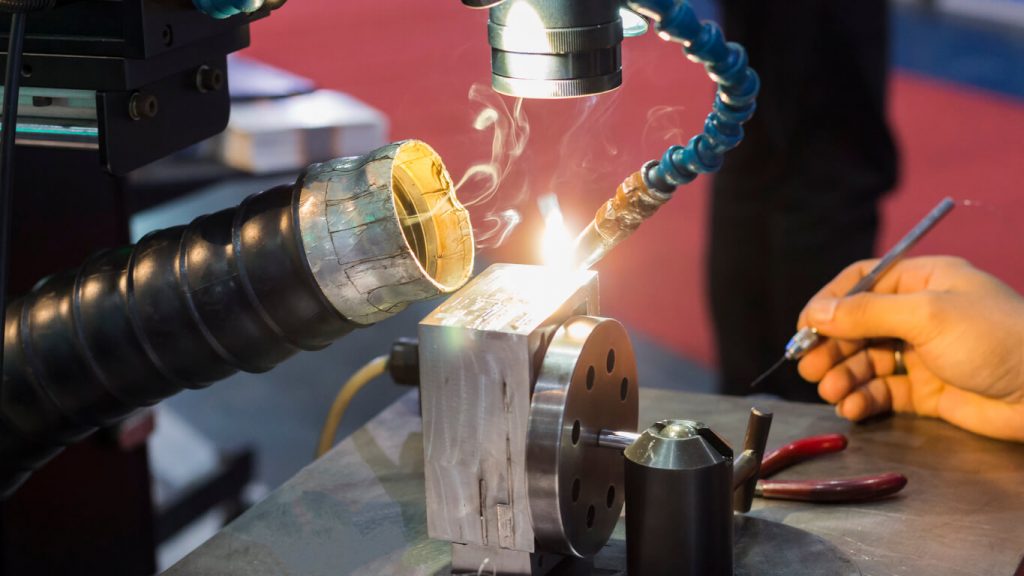
For welding thick objects, a continuous laser is advised
It works very well on refractory metals. If applied to metal or a part that is too thin, it may cause issues. In certain circumstances, the laser may harm, distort, or melt the component. Although it is more costly than a pulsed laser, the operational expenses are lower.
How should the laser beam source be selected?
The Nd: YAG laser, CO2 laser, and fiber laser are the three different sources. Depending on the kind of laser you select, you can choose different sources (pulsed or continuous).
Using a fiber laser
This method is based on narrow, pointed beams that enable continuous, penetrative work. The fiber laser can quickly and effectively cut through thick sheets, just as the CO2 laser. In terms of usage and maintenance, it is simpler to incorporate into a machine than other lasers. This laser provides a typical efficiency of 25%. Using a CO2 laser
This method makes use of an electrically-excited, nitrogen, helium, and carbon dioxide gas combination that is designed for continuous operation. The CO2 laser can quickly and effectively cut through thick sheets, much like the fiber laser.
It is more extensively used than the fiber laser because it is better at piercing thick steel items. Compared to the fiber laser, it is more flexible and can cut through both thicker and lighter materials. For 8,000 W, this laser has an average efficiency of 7%.
Which welding machine configuration should I pick?
For welding equipment, three different configurations are available:
The manual configuration
- Automatic configuration o Semi-automatic setup
- The configuration you choose will rely on Your production (small- or large-scale?)
- The layout you desire for your workplace.