Content Attributes
A material handling method that is ideal for the storage space of commodities integrated on skids or palettes is warehouse shelving. It often known as store or pallet racking.
It enables optimum space usage while allowing for simple access to stored items for improved inventory control. The blog below will contain all the information you need to know about choosing a warehouse shelving system. Continue reading to find out more.
Overview of warehouse shelving
The warehouse shelving or warehouse rack manufacturers utilize racks to store large quantities of generally non-perishable goods when space limited.
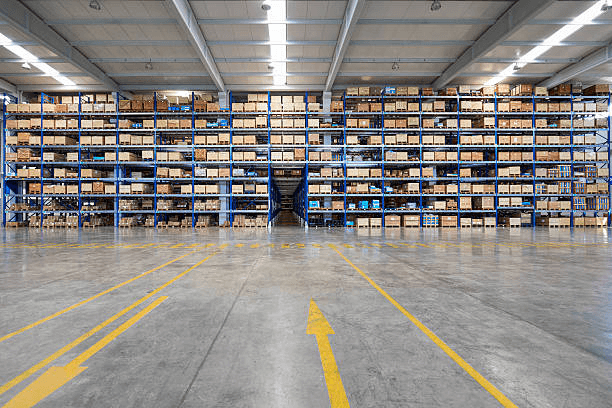
Palletized goods typically stacked up to three levels before becoming unstable and prone to topple. Availability of the required height, a racking system allows the manufacturer to store sold in bulk products up to seven stacks high.
Using a stacking system has several advantages
Racking systems are utilized for raw resources and part storage in addition to finished goods handling. Selected racking can be constructed to allow access to the most incredible amount of objects while maintaining a high level of variation.
In addition, some distribution systems favor the FIFO (first-in, first-out) inventory control strategy. For example, a warehouse shelving system gives you access to the older things in your warehouse inventory, allowing you to offload them first.
Aside from maximizing storage space, warehouse shelving has several other advantages. These advantages can measured in financial value or savings resulting from the lease of more storage space, reduced personnel effort, and increased throughput.
Compliance with safety regulations and quality management, on the other hand, are additional value-adding characteristics that do not automatically convert to cost reductions. The advantages of a warehouses racking system are listed below-
Adequate storage space utilization:
As previously said, ratcheting wants to take advantage of the otherwise underutilized vertical space. Warehouses designed to hold racks have high ceilings to accommodate frames with many bays.
In comparison to stockpiling, racking allows for easier inventory management. Collecting makes it very impossible to store goods with many different types without taking up many floor areas. Selective racking is a sort of racking system that allows various goods to be kept while consuming the least amount of space possible.
Fewer damaged items:
Clearing systems are aimed at keeping goods contained while minimizing damage. Repacked loads are not stacked on top of one another, reducing touch. There’s also no need to move commodities around to provide people access to hidden goods in a stockpiling. Damage is reduced when there is minor touch.
Increased staff productivity:
The vacant pallet position in a conveyor system may be easily located and accessible. This enables the removal of minor, inconsequential movements that add up to significant losses over time.
Storage automation:
The first stage in warehouse automation is to adapt a racking system. This is accomplished by using guided forklifts and cranes and smart conveyor systems. This can save money on staff and streamline the business process, which is especially beneficial for large distribution centers.
Clearing systems are safe as long as they are correctly built. Equipment and other high-quality elements can be used to make beams and columns. The steel structure, which is absent in most storage systems, leads to stacking things.
Furthermore, safety mechanisms such as activity or motion detection and sirens can be installed on racks for protection during loading and unloading of the item in warehouse shelving.