Content Attributes
Every manager in an organization shares the same goal, to streamline the workflow and eliminate unnecessary and repetitive tasks. This helps them in planning and executing projects effectively and efficiently. To attain such goals, managers use various technologies and methodologies, one of them being “Lean Six Sigma”.
The inception of Lean Six Sigma took place in the United States when the US managers adopted some Japanese manufacturing principles. The objective was to compete with better Japanese products, as a result. Lean Six Sigma was introduced, combining the independent principles of Lean and Six Sigma.
Many successful companies are already implementing LSS principles in their day-to-day operations by relying on professionals with expertise and Six Sigma certificates. One of the most preferred certifications in Lean Six Sigma Black Belt Training.
Such certifications prove an individual’s commitment to improving business acumen & analytical skills. They also open doors to promotion into the upper management. According to Indeed, Lean Six Sigma green belt practitioners earn up to $96,350 per year and will earn more as they climb up the hierarchy.
In this article, we will discuss what Lean Six Sigma exactly is and its basic principles and fundamentals.
What is Lean Six Sigma?
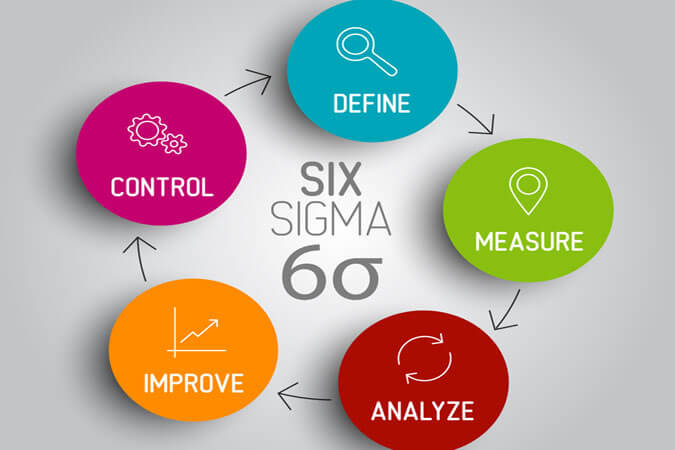
- Lean Six Sigma is an approach that seeks to improve performance by eliminating waste and defects and assuring quality in production and organizational processes.
- It combines two of the most popular quality management methodologies, Lean and Six Sigma.
- The purpose of the Lean methods is to define and reduce waste, and Six Sigma is known for process improvement.
- The Lean Six Sigma blends into two approaches, one is the refinement of the production process and the other is the reduction of 8 wastes analyzed by the Lean method.
- By paying careful attention to how waste affects production processes, business leaders can take significant strides toward optimizing their operations.
- Some of the benefits of implementing Lean Six Sigma are increased profits. A standardized and simplified process, reduced errors, employee development, and value to customers.
To understand Lean Six Sigma, let’s understand Lean and Six Sigma principles separately. You can even check out Simplilearn online courses to understand the topics that makeup certifications’ course curriculum.
Lean Principles
The Lean principles focus on providing value to the customers, eliminating waste, continuous improvement, and reducing the cycle time. With the help of Lean methods, businesses can identify the wastes and handle them. According to the Lean methodology, there are 8 kinds of waste, abbreviated as ‘DOWNTIME’. By using a value stream map for documenting the steps involved in producing a product or delivering a service, Lean sets out to identify and eliminate that waste.
For many years now, many businesses have started to identify and handle different kinds of waste through Lean methods. The 8 wastes that are abbreviated as DOWNTIME are Defects, Overproduction, Waiting, Non-utilized talent, Transportation, Inventory, Motion, and Extra-processing.
- Defects – It is the waste that is created by a product or a service that fails to meet the customer’s expectation.
- Overproduction – It is the waste created due to producing more products than required.
- Waiting – It is the time wasted on waiting for information, instructions, materials, bills, or equipment.
- Non-utilized talent – It is the waste of human potential, underutilizing capabilities, and delegating tasks to people with inadequate training.
- Transportation – It is the waste created by the excess movement of people, tools, equipment, inventory, and other components of a process than required.
- Inventory – This is the waste that occurs due to having more products and materials stored in the inventory than required.
- Motion – This refers to time and effort wasted due to the unnecessary movement of people, equipment, or machinery.
- Extra-Processing – It refers to more work, more components, or more steps in a product or service than required.
Six Sigma Principles
Six Sigma is a set of tools and techniques that are used to improve the process. There are 2 principal methodologies in Six Sigma, DMAIC, and DMADV. Lean Six Sigma relies only on the DMAIC methodology.
DMAIC is an acronym for Define, Measure, Analyze, Improve, and Control. To understand how it helps to improve the existing products and processes. Let’s take an example of the supply chain issues in the supermarket. Which are causing delays in the morning delivery of milk.
- Define – In the define phase, we determine the goal of the project. In this case, the goal is to reduce the amount of time taken from the warehouse to the supermarket to deliver milk. So that they stock the milk on the shelf before 8.30 am.
- Measure – In the measure phase, we measure the performance of the current, unaltered process. The milk truck leaves at 7.30 in the morning and has two routes to reach the supermarket. Route A is the current preferred one as it takes 60 minutes. Whereas Route B takes 70 minutes to reach the supermarket.
- Analyze – In the analysis phase, we figure out why the defects exist. We analyze and see that Route B takes 70 minutes because of the traffic. As it is the school bus route. But if the milk leaves the warehouse at 6.30 am, instead of 7.30 am. Then they can avoid the traffic and reach the supermarket in 40 minutes. Whereas Route A will still take 60 minutes.
- Improve – In the improvement phase, the process can be improved by addressing and eliminating the root cause. We know that advancing the milk pick-up by an hour and taking Route B instead of Route A can save time. So we can change the process accordingly, providing the workers ample time to stalk the milk on the supermarket shelves, before the morning rush.
- Control – In the control phase, we make regular adjustments to control new processes and future performances. So we’ll continue to monitor the delivery time and try out any alternative routes to continuously improve the process and ensure even faster delivery.
Now, this process change helped reduce the time taken & cost and enhance the shelves and customer retention.
Lean Six Sigma not only reduces the process defects and waste but also provides a framework for overall organizational culture change. By introducing the principles of Lean Six Sigma, we can change the mindset of the employees to focus on growth and continuous improvement via process optimization. This change in culture and an organization’s mindset maximizes efficiency and increases profitability.