Content Attributes
There are many ways to minimize hazards in your warehouse. You can safeguard equipment between the worker and conveyor. Keep aisles and passageways clear and in good condition, and include warning signs to prevent people from getting near docks. And since forklift truck accidents are prevalent and potentially fatal. It’s always a good idea to ensure operators are competent and that the equipment is in great working condition. If the warning lights are not working, you should order a forklift blue light and replace them immediately before getting the equipment back into operation.
Warehouse safety is not an option but a necessity. When the warehouse is not safe, the employees become exposed to unnecessary hazards. That could result in severe injuries and sometimes even death. Unfortunately, this can only make you vulnerable to lawsuits that will leave you and your business broke. Besides, regulatory bodies like OSHA require all warehouses to maintain specific safety standards to keep everyone safe. If you are not meeting these standards, you may end up closing shops or paying a hefty fine. With that in mind, let’s now look at some safety tips: how to minimize hazards in the warehouse.
Forklifts
Forklifts play a critical role in warehouses and storage facilities. They help to quickly and easily move loads of goods within the warehouse and also during the loading and unloading of goods from train cars and transport trailers. However, when they are not operated correctly, they can cause serious accidents, thereby destroying properties and harming the operators and workers.
In fact, OSHA cites unsafe use of forklift as the leading hazard in warehousing operations. To secure your forklift, you need to ensure that all its lightings are working optimally. If the blue lights are damaged, order forklift blue light right away. Do not postpone. Additionally, you should ensure that those operating the forklift are well-trained and experienced to do the work. And don’t leave it at that – keep training and evaluating them from time to time to ensure they remain competent.
Conveyors
Conveyor systems used in warehouses to increase productivity and material handling capacities. They also improve worker safety, because it negates the need for the carrying or handling of heavy or hazardous loads manually. But as with forklifts and other equipment, conveyors can cause injuries when not carefully handled. So, to keep your team safe from conveyor accidents. You have to ensure that they well-trained and informed.
Make sure they understand that conveyors are for materials and not people – so, they shouldn’t climb, walk, sit, stand, or misuse the conveyor. Additionally, they shouldn’t overload a conveyor because this may cause malfunction, overheating, among other damages. You can also ensure warning labels are in place and that workers wear the right clothing.
Loading dock
The loading dock is the main area where goods are moved in and out of the warehouse. They are notoriously dangerous because of the use of heavy machines and equipment like trucks, trailers, and forklifts. OSHA estimates that forklift and other heavy equipment cause about 35,000 injuries annually. About 25% of all reported injuries in warehouses happen on the dock. Some common loading dock hazards include lifting injury, slipping or tripping, forklift malfunctions, unsecured loads, sharp objects and edges, and injury from heavy machinery.
But luckily, most of these accidents can be prevented with proper safety measures in place. Tips for loading dock safety include using visual doc communication, cleaning loading areas regularly, securing loose products, and using locking devices on every truck. On top of that, you should mark floors with tape to identify areas where walking is off-limits, educate your team about dock safety tips and rules, and put padding on edges of sharp corners.
Implementing Technological Solutions
How does your warehouse make use of technology to ensure workplace safety? Though it’s not a common practice, the new normal has seen the advancement of new technological solutions that could help ensure safety. These solutions can be beneficial for warehouse management, especially now with consumer demand for e-commerce products reaching a new peak.
There are now innovative technological solutions, such as apps and software, that gather behavioral data through employee behavior monitoring and that single out behaviors that may influence safety in the warehouse or in any work environment. Using this data, you can closely monitor safe and unsafe practices. This will allow you to develop the right action plan to improve safety processes and ensure quality, productivity, and safety.
Certain safety monitoring apps and programs can downloaded on mobile devices. So warehouse managers can easily track and assign activities while ensuring compliance with safety protocols. This can also allow quality control specialists to observe existing and adjacent issues in advance, reducing product damage and safety risks.
If you’re thinking of getting a technological solution for your warehouse, you have a lot of options to choose from. Many technology providers offer different apps and programs to ensure a strong warehouse safety foundation nowadays. You can easily choose a provider that provides excellent environment, health, and safety (EHS) solutions and services. For instance, ETQ offers EHS solutions that provide in-depth safety hazard analysis and monitoring. Just remember that, as you look through the different options available, you should consider which one best fits your warehouse’s needs.
General warehouse safety tips
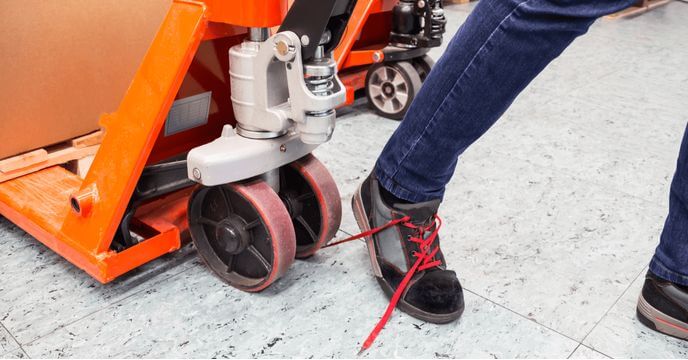
Label all areas correctly
As much as you have educated your teams about warehouse safety, make sure to label all areas so that people can warn of potential danger. Using warning lights on forklifts is also a great idea as it will notify workers about an arriving forklift, or areas they shouldn’t go beyond.
Ensure safety equipment used every time
Safety equipment – including eyewear, helmets, boots, and fitting clothing – minimizes workplace injury. Your team should also avoid lifting heavy and/or hazardous items, especially when they can use hydraulic dollies or forklifts to move these items.
Eliminate any potential safety hazard
Make sure all warehousing floors are dry and free from stumbling hazards. Perform routine checks to fix any glaring problem before it causes an accident. Fix any pits and crack in the floor, and fit lighting on dark spaces to illuminate the area.
Conclusion
When safety procedures implemented correctly. The business thrives because of infrequent machine breakdowns, motivated employees, and fewer lawsuits. Besides, the peace of mind that comes with knowing everything is running as expected is insurmountable.